Greg Lowe from Lowes TC is on a mission to automate tissue culture production, making it more affordable to produce high health clonal plants in this country. Find out about his business’ new TC+TM liquid media temporary immersion system bioreactor and automated production systems.
by Gabrielle Stannus
Greg Lowe is the Director of Research & Development at
Lowes TC, an Australian owned business specialising in plant tissue culture propagation. Lowes TC currently supply over 100,000 plants a week for the Australian industry. However, Greg believes that Lowes TC can produce many more plants through automation.
“Commercial plant tissue culture (TC) started in the early 1960’s. Today’s lab looks the same as then. It has a high labour input with little to no automation. Not surprisingly, the international TC industry has mainly located to low wage countries,” says Greg. Despite increasing demand for high health clonal plant propagation (HHCPP) in many countries, TC production continues to remain expensive when compared to alternatives such as unrooted cuttings (URCs).
Greg claims that URCs can be produced for as little as five to ten cents in some countries, factoring in a couple of extra cents for air freight and other costs. He estimates that every plant that comes out of TC production in Australia has between 30 to 50 cents worth of labour in it. TC therefore cannot currently compete with URCs on cost, especially when existing TC systems are limited to producing around 200 plants per hour.
Lowes TC+TM Bioreactor - Patented technology
Over the last three years, Greg has been researching methods to improve and automate TC production. However, Greg found that none of the existing protocols using small jars of agar in them worked with the automation that he had in mind.
“We basically came up with a liquid media temporary immersion system bioreactor. It is called a temporary immersion bioreactor because pressurized air moves the liquid media up into the plant growing chamber for a few minutes every eight hours. This liquid media waters and fertilises the plants before draining away. The plants therefore remain in a dry environment so that they can grow normally,” Greg says.
Although liquid media bioreactors have been around since the 1970’s, existing products do not allow for easy automation. To avoid hygienic seals breaking under high pressure, these bioreactors have chambers with small openings fitted with a rubber seal tightened onto a screw thread. This small opening makes it difficult to remove the plants from the chamber without contaminating the plant.
“We had to figure out a way of moving media into the growing chamber and out of it without using high pressure air. We cut the container in half at the widest point and put a big seal all around it so that we can open it up and have complete access to one hundred percent of the container from above. And that access allows us to then use the automation,” Greg explains.
Lowes TC Automated Propagation
“We realized what we could do with the automation is improve the materials handling process. Every time we touch the bioreactor, we are moving 150 or 400 plants, so we are not touching them one at a time. We touch them in mass, and we produce them in mass,” Greg says. Lowes TC automated propagation involves a simple materials handling process using conveyors and pick and place tools. It does though have the potential to be fully automated with robots.
“With the control that we can get in our TC+TM bioreactors, we can increase the air flow in the bioreactor, and we can start to harden the plant. Through the automation process, we can also put the plants into a growing medium in a plug tray inside the container and start the roots developing in a normal plug mix. The cuticles start to harden, and the stomata start to work. They are still softer when they come out than a normal plant out of a greenhouse. However, they are much hardier than a tissue culture. And because they are already in a little plug tray, you don't have to plant them by hand. You just put them into an existing automation system,” Greg explains.
Accelerating Commercialisation Grant
“Everyone who has actually seen the automation process has the same reaction. They say, hasn't someone thought of this before?”, says Greg.
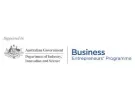
The Federal Government agreed, awarding Lowes TC an
Accelerating Commercialisation Grant to build a pilot plant and develop further prototypes. Lowes TC received more than $880,000 matched funding through the Department of Industry, Innovation and Science Business Entrepreneurs' Programme.
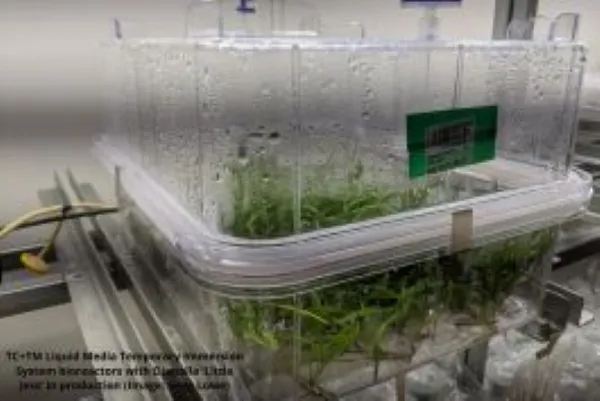
The pilot plant currently contains around one thousand bioreactors in which more than one hundred plant genera are being tested. The first two crops to complete an entire production run in the TC+TM bioreactor were dianellas and lomandras, popular landscaping plants. “We previously had issues with Dianella ‘Little Jess’. It was not very profitable in normal tissue culture. We put it into the TC+TM system and we have turned that around completely. It really made a huge difference. Now all our Dianella ‘Little Jess’ is produced in the new system,” says Greg.
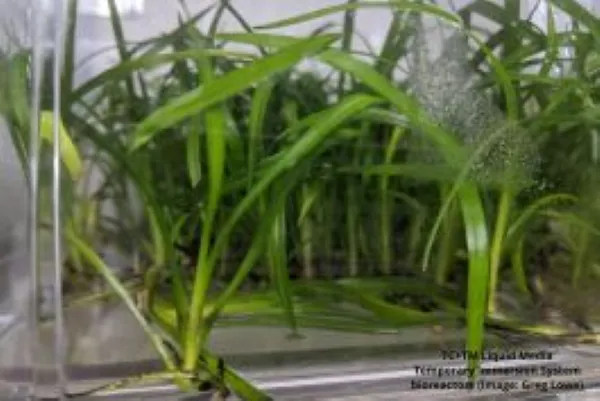
Commercialisation plans
Greg claims that this new bioreactor technology will double the capacity of Lowes TC’s Tumbi Umbi facility. It has already increased yield by 100% on some crops and reduced the labour cost by up to 30% on some crops during trials. He believes that this technology has the potential to replace a lot of URC and seed production.
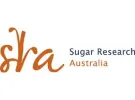
Lowes TC recently signed a licence allowing
Sugar Research Australia to use its new technology to produce sugarcane within Australia for the next 10 years. Sugar Research Australia have also committed to putting on a researcher at their Brisbane office to work on developing protocols for sugar cane within the TC+TM system.
With patents pending in Australia and overseas for both Lowes TC growing and automation systems, Greg is keen to discuss potential collaboration with other propagators within the productive, forestry and ornamental sectors of horticulture. “It's a huge, huge industry and we basically feel that there's a lot of potential if we can get the volumes right. However, we do not want to become a giga factory. We just want to license our technology, see if it works for you, and figure out how to get that and to collect a very small royalty per plant. So that is our commercialisation plan,” Greg explains.